A warehouse control system (WCS) is a software application designed to direct the activities of automated material handling equipment (MHE) within a warehouse. Think of it as a traffic cop for automated sorters, packers, conveyors, and robotic systems.
A WCS typically works within a warehouse management system (WMS), which oversees broader warehouse processes like layout optimization, labor management, inventory management, and order processing.
The key difference between these two types of warehouse software systems is in their scope. A WMS has a broad scope and manages all aspects of the warehouse strategy while a WCS controls and optimizes specific tasks related to automated warehouse equipment. In highly automated, large warehouses, a warehouse execution system (WES) may also be used. A WES focuses on warehouse processes, acting as an intermediary between the WMS and the WCS, to maximize workflow optimization and resource utilization.
In this article, we explore the critical role of WCS in improving performance in modern warehouses.
Key Features and Functionalities of a WCS
A WCS, which often includes real-time data processing software, database management systems, and integration middleware, manages the seamless data flow between different platforms and systems. It orchestrates the operation of these two warehouse systems:
- Hardware: Conveyor systems, automated guided vehicles (AGVs), ASRS systems, goods-to-person systems, robotic arms, sorting systems, barcode scanners, and RFID readers.
- Communication: Wireless communication networks, RF communication, cloud connectivity, SCADA systems, HMIs, and programmable logic controllers (PLCs).
Warehouse control software can work in several different configurations. They can be cloud-based or on-premise systems. Some work as standalone systems while others are integrated with a WMS.
Here are the key functionalities of a WCS:
- Material Handling Equipment (MHE) Control: A WCS controls and monitors MHE like automated storage and retrieval systems, automated guided vehicles (AGVs), and other automated equipment.
- WMS Integration: Acts as a bridge between the WMS and warehouse operations by receiving instructions from the WMS and executing them.
- Routing and Flow Control: Optimizes the movement of goods by calculating the most efficient routes and directing MHE accordingly.
- Load Balancing: Ensure efficient use of MHE by distributing tasks and balancing workloads across multiple systems.
- Data Exchange: Facilitates the exchange of real-time information and insights between the WMS, WCS, and other warehouse systems.
Benefits of Implementing a WCS
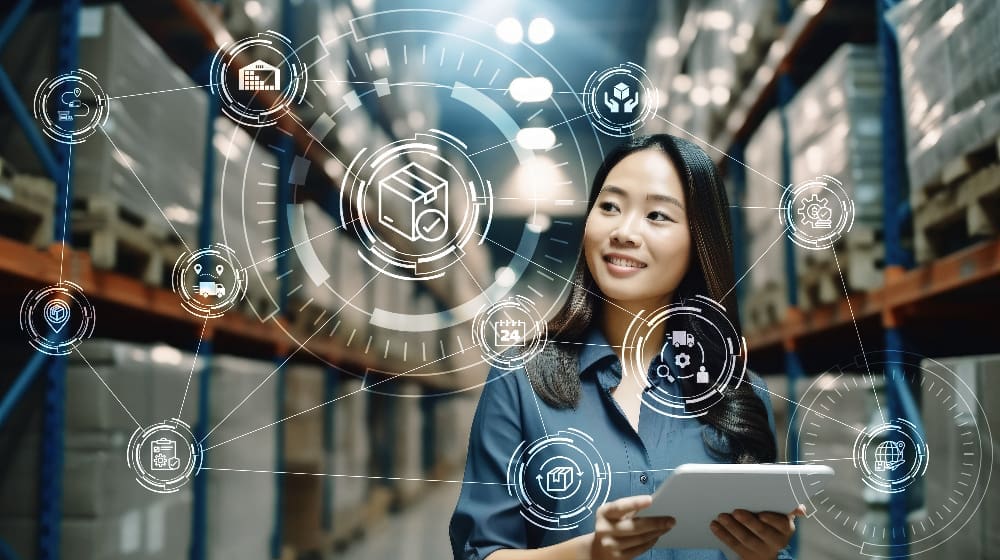
Implementing a WCS offers numerous measurable benefits.
Increased Efficiency and Productivity – A WCS automates manual tasks such as MHE routing to optimize inventory control. This leads to faster and more accurate operations.
Improved Accuracy – A WCS provides real-time inventory tracking and control to ensure accurate movement of goods within a warehouse and minimize discrepancies.
Scalability and Flexibility – A well-designed WCS can adapt to changing business needs like seasonal peaks and troughs and handle fluctuating order volumes seamlessly.
Better Customer Service – Warehouse control systems help businesses process orders faster and ship them out in the shortest possible time. This leads to positive customer experience and satisfaction.
Cost Reduction – Automation and optimized workflows can help cut down on labor costs, minimize errors and waste, and reduce energy consumption and utility costs.
Selection Criteria for Choosing a WCS for Your Business
Let’s now examine the key considerations for selecting a WCS for your warehouse business.
- Warehouse Size: A simple and cost-effective WCS may be sufficient for small and medium-sized warehouses. Larger warehouses with complex workflows require a robust WCS with extensive integration.
- Level of Automation: A WCS with basic device control is sufficient for warehouses with minimal automation. Highly automated warehouses will need an advanced WCS with advanced integration and flow management.
- Throughput: A simple WCS is enough for warehouses with lower order volumes. Those with higher volumes and operational speed need an adaptable WCS with real-time data processing ability.
- Budget: An entry-level WCS may be suitable for businesses with minimal automation. Those with bigger budgets can invest in a feature-rich WCS with advanced integration capabilities.
- Scalability: Businesses that do not plan on significant expansion can choose a WCS that meets current needs. Those who foresee expansion and more complexity must choose a WCS that offers reliable scalability.
Future Trends in WCS Technology
The future of warehouse control systems is deeply intertwined with advances in AI, IoT, cloud computing, and data analytics,
Let’s examine the future trends in WCS technology in some detail:
Increased Integration with AI/ML Systems: The next generation of WCS will increasingly leverage AI and ML to optimize warehouse operations through data-driven decision-making.
Greater Use of the Internet of Things (IoT): IoT sensors will play a pivotal role in enhancing real-time data collection and monitoring, enabling smarter automation, and providing more accurate inputs for predictive maintenance.
Edge Computing: As more devices and sensors generate larger amounts of data, edge computing will enable WCS to process data closer to the source to reduce latency and improve decision-making.
Sustainability and Energy Efficiency: Future WCS will integrate energy management features to reduce the energy consumption of automated systems. Excess stock and waste will be minimized with lean inventory systems and just-in-time fulfillment.
FAQs About Warehouse Control Systems
What are the functions of a warehouse control system?
The key functions of a WCS include control of automated devices, real-time monitoring of equipment and inventory, task scheduling and prioritization, and integration with other warehouse systems and platforms.
What are the 4 basic functions of a warehouse?
The four basic functions of a warehouse are:
Receiving goods.
Storing goods.
Picking and packing orders.
Shipping orders.
What is a warehouse controller?
A warehouse controller is a specialized software or hardware system responsible for overseeing and optimizing the flow of goods in and out of a warehouse.
Improve Efficiency in Your Warehouse with PrecisionWare 360
Precision Warehouse Design specializes in the design, layout, and implementation of warehouses and distribution centers. We provide comprehensive services, tailored solutions, and advanced warehouse control software for businesses across the US.
Get in touch with us today to transform the efficiency and functionality of your warehouse operations.